TATA Steel in Thailand moves closer to its vision of zero failures
Thailand is aiming to enhance its status as a regional logistics hub and for that it needs to continue investing in transport infrastructure and urbanization; this requires steel.
Production of steel is an energy-intensive manufacturing process that needs efficient and reliable electricity supply. The steel-making process starts with melting of iron ore or recycled steel and ends with products such as steel coils, plates, sections or bars. The manufacturing processes requires high currents that enable extremely high temperatures and frequent on- and off-switching for rapid cool down. These huge fluctuations in power consumption create voltage variations, stressing the electrical infrastructure, including transformers, to their limits.
Transformers are critical assets in electrical networks. A transformer outage can cause substantial loss in industrial production, for example if a furnace starts to cool down when it is not supposed to. Setting up smart condition monitoring and diagnostics for the transformer fleet and maintaining it efficiently is critical to prevent power outages and avoid loss of production.
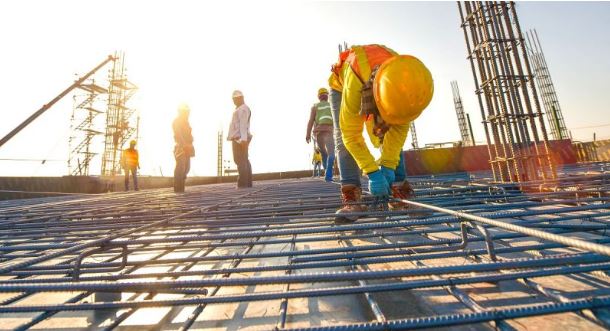
Tata Steel in Thailand is adopting intelligent devices and asset health management software from Hitachi ABB Power Grids open TXpertTM Ecosystem[1] for transformers in three of its manufacturing facilities[2]. These will provide actionable insights on the operational health of the fleet and help to reduce costs and risks, optimize operations, extend life-expectancy and enhance environmental performance.
“Power transformers are crucial for enabling the steel-making process. It is very important for us to understand the condition of the transformer fleet to minimize the loss of revenue prolonging the time-between-failure and avoiding long time-to-repair,” said Dr Aree Wangsupphaphol, Department Manager – Maintenance Expert Group, Tata Steel Thailand. “The TXpertTM Ecosystem from Hitachi ABB Power Grids immediately caught our attention as it delivers the high-performance characteristics and features needed to digitalize our transformers and achieve our vision of zero failures. To start with we, decided to install the CoreSenseTM M10 in one of our refurbished 72 MVA transformers. We are satisfied with the field performance of the unit and the ease of use. After very stringent assessment of several vendors, we decided to award the order for several CoreSenseTM M10 multi gas and CoreSenseTM single gas units to Hitachi ABB Power Grids along with the TXpertTM HUB and APM Edge software.”
Hitachi ABB Power Grids experts undertook a detailed study to estimate the benefits of the TXpertTM Ecosystem for Tata Steel, assuming standard operational conditions. The TXpertTM enabled transformers are expected to reduce downtime and failure rate by about 60% and increase life expectancy by about 35%. A substantial reduction in maintenance costs and time is also expected with the move from time-based maintenance to predictive maintenance practices.
Benefits of TXpertTM Ecosystem [3]:
- ∼ 60% reduction in failure rate and asset downtime
- ∼ 35% increase in transformer lifespan
- Reduced maintenance costs and time
[1] Project scope of Hitachi ABB Power Grids supply to TATA Steel Thailand:The digitalized transformers will be equipped with TXpert™ Hub (CoreTec™ 4), which will analyze data coming from TXpert™ Ready sensors. These sensors include Hitachi ABB Power Grids CoreSense™ and CoreSense™, M10, digital devices for tracking the level of dissolved gases and moisture levels in transformer oil. Intelligence and data collected from the above will be collected and further analyzed with help of Hitachi ABB Power Grids APM Edge asset performance-management software, ensuring that these critical assets are always available and utilized optimally.
[2] TATA Steel Thailand is one of the largest manufacturing facilities in Thailand and currently operates three manufacturing plants – The Siam Construction Steel Co. Ltd (SCSC), The Siam Iron (2001) and Steel Co. Ltd (SISCO) and Tata Steel Manufacturing (Thailand) PLC. (TSMT).
[3] Numbers were calculated specifically for TATA Steel Thailand and can also be calculated to support other customers according to their needs and operating conditions.